Overcoming Challenges of Dry Docking in China
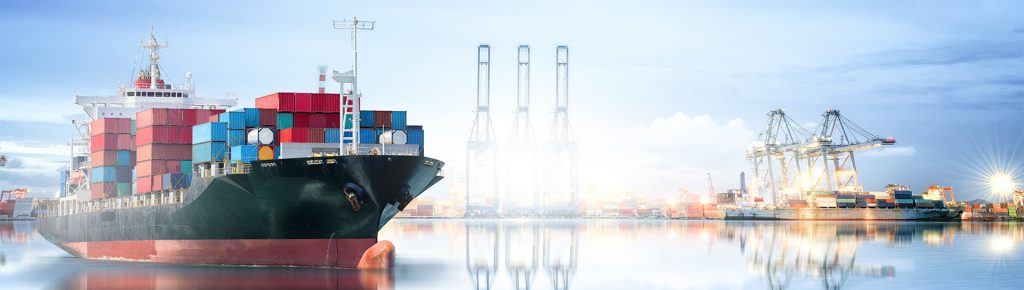
- The Benefits of Local Support for Vessel Repairs in China
Managing vessel repairs, servicing, and maintenance at Chinese shipyards can often seem like a daunting task, especially when you’re facing challenges such as communication barriers, navigating local regulations, and dealing with logistics. However, one key factor can make all the difference: local support.
Having a local team on the ground in China not only helps you reduce downtime but also enhances the efficiency of the entire repair process. Here’s why:
Faster Communication & Response Time: Our team is local, meaning you’ll never have to deal with time zone delays or language barriers. We respond quickly, keeping your project on track.
Navigating Local Regulations: Compliance with local laws is critical. Our experience with Chinese regulations ensures your vessel meets all necessary requirements.
Cost Savings: With established relationships in the region, we help negotiate better pricing for parts and services, keeping your project within budget.
Adaptability: Projects rarely go exactly as planned. Our local expertise helps us quickly adjust to schedule changes or delays, minimizing disruption.
Local support is more than just a convenience—it’s a necessity. Let us help optimize your vessel’s repair process in China.
- How Pre-Installing Applications Can Streamline Drydock Operations
The drydock period is a critical time for vessel maintenance, and every minute counts. One effective way to minimize downtime and streamline operations is through pre-installation of applications and server setup. Here’s how our pre-installation services can make a significant difference:
Faster Setup: By preparing the applications and configuring the server at our office beforehand, we save valuable time during drydock.
Reduced Workload on Site: With the technical groundwork already completed, there’s less need for heavy lifting during drydock, freeing up your team to focus on other critical tasks.
Seamless Transition: This proactive approach ensures that the application setup goes smoothly once the vessel arrives at the shipyard, reducing the risk of delays.
Pre-installation is a small step that makes a big difference in the overall success of your project. Learn more about how we can streamline your drydock operations!
- Top Challenges in Vessel Maintenance at Chinese Shipyards (And How We Solve Them)
Vessel maintenance in China comes with unique challenges that can create significant roadblocks if not properly managed. Some of the most common hurdles include:
Language Barriers: Communication issues can lead to misunderstandings. We’re fluent in both English and Chinese, ensuring smooth coordination with shipyards.
Regulatory Complexity: Navigating local laws and regulations can be daunting. Our team is well-versed in Chinese maritime regulations, ensuring compliance and avoiding delays.
Logistical Issues: Shipping delays and customs complications can cause headaches. With our local connections, we manage logistics seamlessly to prevent disruptions.
These are just a few examples of the challenges we help vessel owners overcome. Our local expertise and proactive approach ensure that your vessel’s repair project runs as smoothly as possible.
- Why Choose China for Vessel Repairs: A Cost-Effective Solution
When it comes to vessel repairs, China offers a unique combination of cost-efficiency and high-quality workmanship. Here’s why more vessel owners are turning to Chinese shipyards for their repair needs:
Competitive Pricing: Labor and material costs in China are often lower compared to other regions, allowing you to get more value for your investment.
Skilled Workforce: China is home to a highly skilled workforce that is experienced in handling complex vessel repairs and maintenance projects.
High-Quality Standards: Despite lower costs, Chinese shipyards maintain rigorous quality standards to ensure your vessel is in top condition.
Choosing China for vessel repairs is not only a cost-effective decision but also one that can help you maintain the highest standards for your vessel.
- How We Help Manage Schedule Delays and Unexpected Changes in Drydock Projects
In the world of vessel repairs, delays are inevitable. However, how you handle those delays makes all the difference. Our team is equipped to manage schedule changes and unforeseen issues without losing momentum.
Here’s how we tackle these challenges:
Flexibility: We understand that vessel repair projects don’t always go as planned. Our team quickly adapts to schedule changes, ensuring minimal disruption.
On-the-Ground Support: With our local team in place, we can implement changes quickly and address issues on-site as they arise.
Proactive Communication: We keep all parties in the loop to avoid surprises and ensure that everyone is aligned on project timelines.
Whether it’s a small delay or a major schedule shift, we help you stay on course and minimize any setbacks.
- The Role of Local Expertise in Managing Vessel Repairs and Servicing
Navigating vessel repairs without a local team can be challenging, especially when dealing with complex logistics, regulations, and technical issues. That’s where local expertise comes in.
Our team’s deep knowledge of the local landscape in Chinese shipyards allows us to:
Ensure Efficient Operations: We understand the local systems, ensuring smoother coordination with shipyards and suppliers.
Troubleshoot Issues: From unexpected technical problems to bureaucratic hurdles, our local expertise allows us to solve problems quickly and effectively.
Maximize Resources: We help optimize resources, ensuring you get the best value out of your repairs and maintenance.
Local knowledge isn’t just helpful—it’s essential for efficient vessel repair projects.
- Reducing Costs in Vessel Repairs: The Power of Local Support and Relationships
One of the primary benefits of working with a local team is the ability to reduce costs. Here’s how we help vessel owners save money during repairs:
Better Pricing: Thanks to our long-standing relationships with local suppliers and shipyards, we can secure better pricing on parts, materials, and services.
Efficient Logistics: Our local knowledge helps streamline logistics, reducing the chance of delays caused by shipping or customs.
Fewer Surprises: We understand the local market and can predict and mitigate risks, ensuring no hidden costs pop up during the repair process.
By leveraging our local connections, we help you keep your vessel repair costs low and your project timeline on track.
- Risk Management in Vessel Repair Projects: How Local Support Mitigates Issues
Vessel repair projects are inherently risky, and delays or poor-quality work can result in significant additional costs. Effective risk management is key to minimizing those risks, and that’s where our local team comes in.
We mitigate risks by:
Identifying Potential Issues Early: With our in-depth understanding of the shipyard environment, we can foresee problems before they arise.
Proactive Inspections: We conduct regular on-site quality checks to ensure the repair process is running smoothly and to address any concerns early.
Adaptable Problem-Solving: If an issue arises, we’re able to find solutions quickly, reducing downtime and minimizing the impact on your overall project.
Risk management is all about being prepared. With our local team in place, your vessel repair project will be in good hands.
- How to Ensure Smooth Communication with Chinese Shipyards
Clear communication is essential when working with Chinese shipyards, but language and cultural barriers can often lead to misunderstandings. Here’s how we ensure smooth communication:
Bilingual Team: Our team is fluent in both Chinese and English, allowing us to act as a bridge between your team and the shipyard.
Cultural Understanding: We understand the local business culture and nuances, ensuring that we communicate effectively and avoid common pitfalls.
Real-Time Updates: We keep you informed with regular, clear updates, ensuring that everyone is on the same page throughout the project.
Effective communication leads to faster decision-making, fewer mistakes, and smoother operations.
- Why Working with a Local Team Can Improve Your Vessel’s Repair and Maintenance Efficiency
Vessel repairs and maintenance can be time-consuming and stressful, but working with a local team can significantly improve efficiency. Here’s why:
Quick Decision-Making: Being on-site allows us to make decisions and implement solutions quickly, reducing delays.
Optimized Workflow: Our familiarity with the shipyard process ensures that everything moves smoothly and on schedule.
Immediate Support: Whether it’s a technical issue or a logistical challenge, our team is always available to address any problem that arises.
With a local team managing your project, your vessel repair and maintenance will be faster, more efficient, and far less stressful.
- How Pre-Installing Applications Can Streamline Drydock Operations
The drydock period is a critical time for vessel maintenance, and every minute counts. One effective way to minimize downtime and streamline operations is through pre-installation of applications and server setup. Here’s how our pre-installation services can make a significant difference:
Faster Setup: By preparing the applications and configuring the server at our office beforehand, we save valuable time during drydock.
Reduced Workload on Site: With the technical groundwork already completed, there’s less need for heavy lifting during drydock, freeing up your team to focus on other critical tasks.
Seamless Transition: This proactive approach ensures that the application setup goes smoothly once the vessel arrives at the shipyard, reducing the risk of delays.
Cost and Time Savings: By handling the initial setup and configuration at our China office, we minimize the workload at the shipyard. This reduces the time and costs associated with setup during the drydock period, making the overall process more efficient.
Pre-installation is a small step that makes a big difference in the overall success of your project. Learn more about how we can streamline your drydock operations!